Essentially, Circular Disc (CD) modules are made of a pressure vessel, of a sealing system and of a stack of support plates and membrane cushions
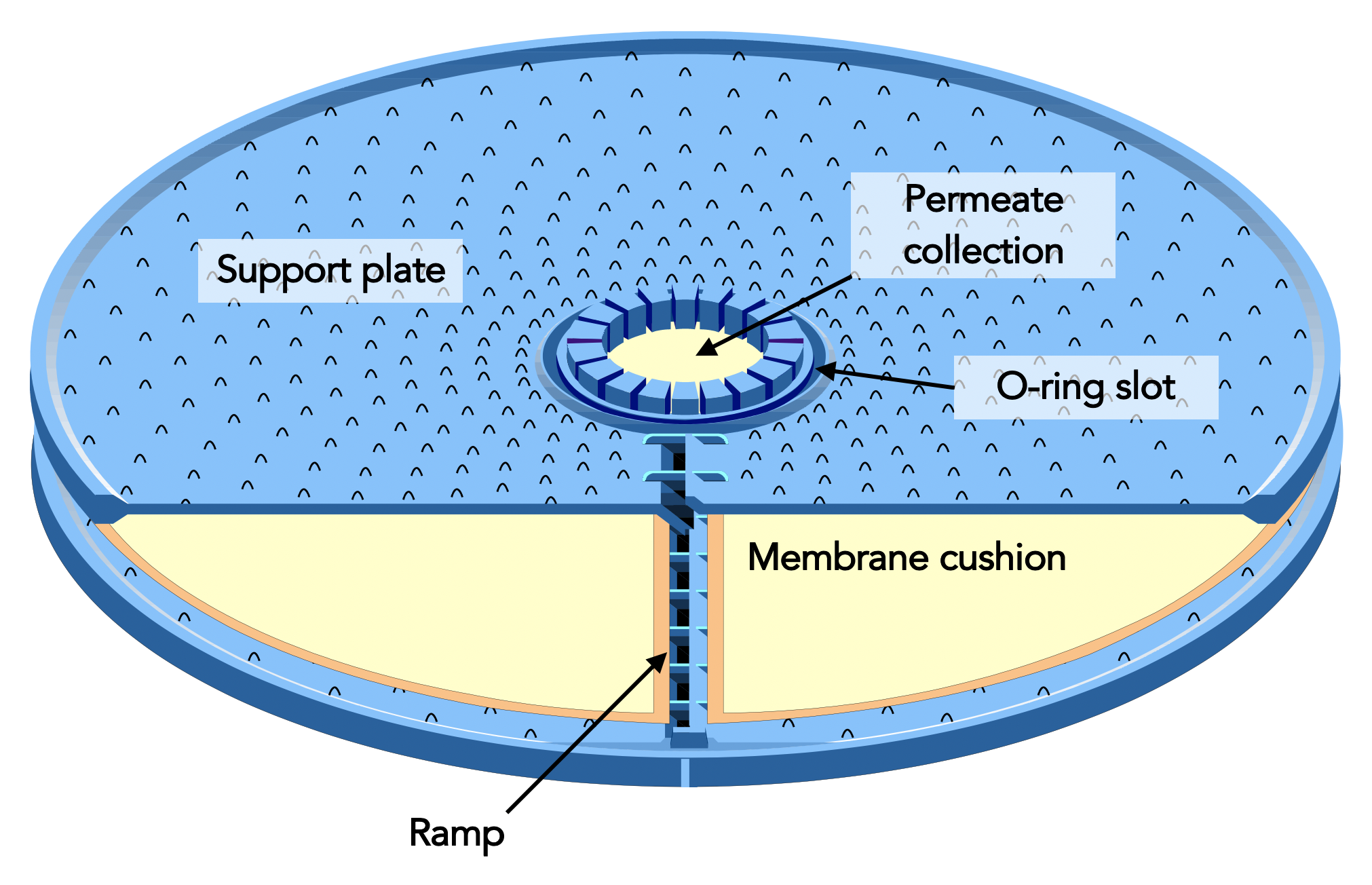
Support plates and membrane cushion
Each membrane cushion is made of two polyamide thin-film composite NF/RO membrane sheets separated by the polyethersulphone permeate spacer. The outer diameter is sealed via thermal welding. The central hole allows the permeate to flow into the permeate collection pipe, while the external slot allows the feed water to flow from one cushion to the next
The membrane cushions are placed in between support plates and O-rings separate the permeate from the feed and concentrate water
The support plates are stacked onto the permeate anchor, which collects the permeate and which is installed within the pressure vessel. The pressure vessel is sealed with pressure plates and end plates and it is connected via dedicated hoses to the feed, permeate and concentrate manifolds. All the connections are all placed on the top end of the CD module
The feed water first flows from the top to the bottom of the CD module within the gap between the pressure vessels and the stack of support plates. Then, it rises along the stack of support plates in a helicoidal pattern, ensuring a steady and well-defined flow regimen on the entire membrane cushions surface. After travelling through the stack of support plates, the feed water is termed as concentrate and it leaves the CD module through the dedicated connection
The permeate crosses the NF/RO membrane sheets into the permeate spacer and it leaves the membrane cushions to the permeate anchor at the center of the module. Then, the permeate leaves the CD module through the dedicated connection
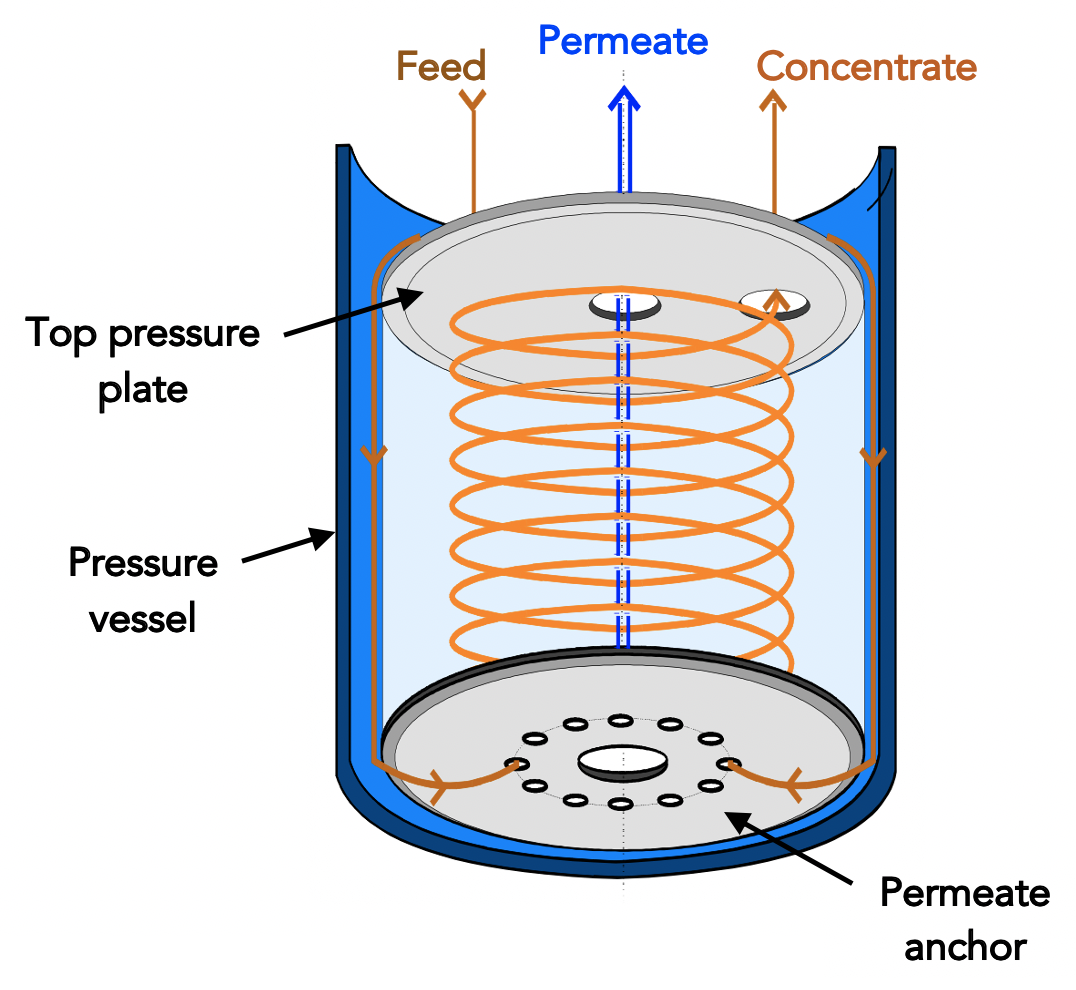
Inside of a CD module
CD modules’ specific advantages are the following:
- wide applicability as it is possible to use any membrane material (as long as it can be thermally welded)
- highest water recovery thanks to the high operating pressures and the optimized hydraulic regimen
- simpler pre-treatments compared to spiral-wound NF/RO elements
- low energy consumption because of low crossflow requirements (compared to tubular NF/RO modules) and of low pressure losses (compared to other plate-and-frame NF/RO modules)
- longer membrane lifetime thanks to the optimized hydraulic regimen (lower mechanical stress, better cake layer and concentration polarization control)
- ease of cleaning due to the optimized hydraulic regimen
- ease of maintenance due to the simpler module construction compared to other plate-and-frame NF/RO modules
- clusterization capability to reduce CapEx and OpEx compared to other plate-and-frame NF/RO modules
In particular, compared to other plate-and-frame solutions, the unique CD module design avoids:
- sharp turns in the feed/concentrate stream as the flow from one membrane cushion to the next follows a 35° flat ramp
- significative changes in the size of the flow channel and, thus, in the flow velocity (which shows a variance of 10%)
Therefore, the module pressure losses and, thus, the pumping power demand are considerably reduced:
Total pumping power consumption in [kW] (10 m³/h @ 70 bar):
Total pumping power consumption in [kW] (10 m³/h @ 120 bar):